- High Output
- Short Lead Time
- Advanced Germany Tech
Single Screw Extruder
Contactor | Schneider brand |
Driving Motor | Siemens AC motor |
Temperature Controller | Omron brand |
Inverter | ABB brand |
Screw and barrel | Bi-metallic or SKD-11 |
Heater | Ceramic heater with SS cover |
Gearbox | Chang brand |
Air Switch | LS brand belongs to LG Group |
BenK Can be Your Trustworthy Single Screw Extruder Supplier in China
BKE25 single screw extruder can be used as co-extruder and lab testing extruder, we use 38CrMoAl material on the screw and barrel, it has high wear resistance, high fatigue strength, and high strength advantages.
Main tech data:
- Lead time: 1month
- Max.output: 3kg/h
- Main motor power:1.5Kw or 2.2Kw
BKE30 single screw extruder is the same function as BKE25 single screw extrusion machine, it has a little higher output than BKE25, it can be used as bigger size plastic pipe extrusion line as strand maker. Welcome to send your inquiry for it!
Main tech data:
- Lead time: 1month
- Max.output: 3kg/h
- Main motor power: 3Kw or 2.2Kw
BKE35 single screw extruder is almost used in small plastic pipe extrusion machine and plastic profile extrusion line, besides, we also can use it as the co-extrusion for plastic profile extrusion line. BKE35 single screw extruder adopt Siemens motor, ABB inverter to keep high-quality performance.
Main tech data:
- Lead time: 1month
- Max.output: 20kg/h
- Main motor power: 7.5Kw or 11Kw
Benk produce the single screw extruder with our owing advanced technology, the single screw extruder is use for PE/PVC/PPR/ABS/PP material, and it also can be used for new and recycled material.
Main tech data:
- Lead time: 1.5 month
- Max.output: 70kg/h
- Main motor power: 18.5Kw or 22Kw
BKE 60 single screw extruder has 38:1 L/D, it belongs high output extruder. It is good at producing PE and PPR pipes. We use high torque gearbox for the BKE60 single screw extruder, the technology is from Germany.
Main tech data:
- Lead time: 1.5 month
- Max.output: 400kg/h
- Main motor power: 110Kw
BKE65 single screw extruder can produce HDPE, PPR, PP pipes with 33:1 L/D, and we can change its L/D as per your output and plastic material. The single screw extruder has an electrical cabinet, vacuum loader and hopper dryer, extruder frame, AC motor, single screw and barrel, ceramic heater and cooling fan, flange.
Main tech data:
- Lead time: 2months
- Max.output: 150kg/h
- Main motor power: 30-55Kw
BKE75 single screw extruder has normal speed and high-speed extruder, their L/D are 33:1 and 38:1, installed 75Kw and 160Kw. Big difference on the output, we recommend use the high speed single screw extruder for plastic pipe extrusion line.
Main tech data:
- Lead time: 2months
- Max.output: 200-600kg/h
- Main motor power: 75Kw or 160Kw
BKE90 single screw extruder means the screw diameter is 90mm, and the screw design difference for different materials and products. We use BKE90/36 single screw extruder to make PP hollow sheet and PP hollow construction board. Where do you want to use the BKE90 single screw extruder in? We will give you the best suggestions.
Main tech data:
- Lead time: 2months
- Max.output: 400-1000kg/h
- Main motor power: 75Kw-250Kw with different L/D and gearbox
BKE120/38 single screw extruder is the biggest high speed extruder currently, maybe we will develop bigger size high speed extrusion machine in the future. It widely used to produce plastic pipes. If you want to invest 710-1000mm HDPE pipe extrusion machine, you can choose it.
Main tech data:
- Lead time: 2months
- Max.output: 1100-1400kg/h
- Main motor power: 315Kw with 38:1 L/D
Single-screw extruder can be used in plastic pelletizing lines for recycling waste plastic, like PE, PP, PET. When single-screw extruder used in pelletizer, the screw design is different with the single screw extrude which used for making plastic pipe and profile. Currently, for recycling project, the screw diameters of single screw extruder start from 100-200mm.
Main tech data:
- Lead time: 2months
- Max.output: 1100-1400kg/h
- Main motor power: 315Kw with 38:1 L/D
Your Premier Single Screw Extruder Manufacturer
BENK single screw extruder also named single screw extrusion machine which is used for plastic processing, the extruder machine is designed by one screw in the barrel. Benk single screw extruder machine has good prices with super quality in all Chinese manufacturers.
Benk single screw extruder is consist of the good brand and quality parts such as gearbox, screw and barrel, Siemens AC motor, Omron temperature controller, ABB inverter
Benk single screw extruder machine can be used to produce PE pipe, PP-R pipe, HDPE corrugated pipe and plastic pellets with downstream machines, such as extruding die, vacuum tank, cooling tank, cutter, and stacker.
BENK has two type of single screw extrusion machine, one is high efficient extruder which has higher production capacity and saves electric consumption for you, the other extruder is normal standard, if you are interested in higher production capacity, pls send email to us.
Benk single screw extruder machine is mostly used for tube extrusion processing, you need to let us know what sizes of pipe you need, and what is your raw material, and how much capacity per hour, then our technical department will design the pipe extruder and extrusion line diagram for you, then you can know how long is the whole plastic pipe extrusion line, and how much square meters of plant you need.
Benk also supplies training and installation for our clients after buying our machine, we also will supply operation guide to our client. If you have trouble with your single screw extruder now, please let us know, we will help you solve it. Thanks.
- Data Sheet
- Videos
- Image Gallery
- Other Main parts
- Send Enquiry
High Efficient Singl Screw Extruder:
Model | KPM60/38 | KPM75/38 | KPM90/38 | KPM120/38 |
Screw Diameter(mm) | 60 | 75 | 90 | 120 |
L:D | 38:1 | 38:1 | 38:1 | 38:1 |
Motor power(Kw) | 110 | 160 | 280 | 315 |
Output(Kg/H) | 465 | 650 | 1100 | 1300 |
increase rate compare with G1 | 20% | 20% | 20% | 30% |
Normal standard Single Screw Extruder:
Model | KPM60/33 | KPM75/33 | KPM90/33 | KPM120/33 |
Screw Diameter(mm) | 60 | 75 | 90 | 120 |
L:D | 33:1 | 33:1 | 33:1 | 33:1 |
Motor power(Kw) | 55 | 110 | 250 | 315 |
Output(Kg/H) | 150 | 330 | 750 | 900 |
waste rate compare with G2 | waste 20% | waste 20% | waste 20% | waste 30% |
Video of Our Single Screw Extruder:
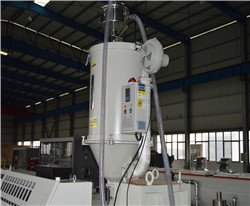

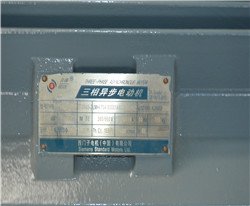

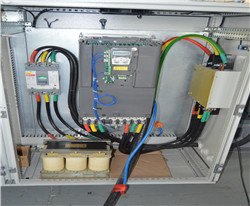
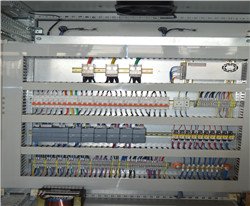
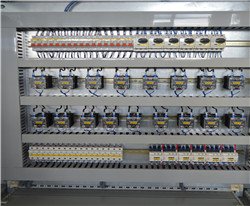

Other Main Parts for Single Screw Extruder:
Name | Brand | Function |
SSR | Crydom Brand with CE certificate | Control temperature for twin screw extruder and extrusion die |
Overload Protector | Schneider Brand(Gv2 type) | Protect fan, the motor in the vacuum pump and water pump |
Fused core | Bussmann Brand | Protect Heater and SSR Relay |
Middle Relay | Ormon Brand | Control Electric Line |
Switch | Schneider Brand | Switch on/off heating function |
Ammeter | CHNT Brand | Checking heating electric line is working or not |
Reactor | Riye Brand | Protect inverter when starting the machine |
24V power source | Ormon brand | used for SSR relay |
Air Switch | LS Brand Belongs to LG Group | Protect Whole Electric Line |
Isolate Transformer | CHNT Brand | Protect staff safe when they operate the machine |
Inverter | ABB Brand | Protect Siemens Ac Motor |
Single Screw Extruder: The Complete Guide
Are you looking for a single screw extruder for your company?
Or are you new in the plastic making industry and you want information about a single screw extruder?
If yes, then you are in the right place.
This guide has everything you need to know about single screw extruder for plastic pipes.
It covers the basic terms of a single screw extruder, parts, how it works and its main applications.
By the end of this guide, you will be an expert in plastic pipe extruder equipment.
Have a look
- What is a Single Screw Extruder?
- Single Screw Extruder Basics
- Advantages of a Single Screw Extruder
- Disadvantages of a Single Screw Extruder
- Parts of Single Screw Extruder for Plastic Pipes Machine
- Single Screw Extruder Designs
- Working of Single Screw Extruder
- Main Applications of Single Screw Extruder in Plastic Pipes Industry
- Support Equipment for Single Screw Plastic Pipe Extrusion
- Single Screw Extruder Specifications
- BENK Single Screw Extruder
What is a Single Screw Extruder?
First, let me begin by defining plastic extrusion.
It is a continuous process that involves melting plastic material, then shaping it into a continuous profile.
For our case, we have the plastic pipes.
Basically, I can summarize this process as:
Figure 1 Plastic extrusion – Photo courtesy: ACPFOTO
Obviously, to achieve this process, you may need different types of machines.
For the scope of our discussion here, you will go for single screw extruder for plastic pipes.
It looks like this – please watch the video below.
Now, back to another fundamental question – what is a single screw extruder?
First, let me begin by saying that a “single screw” is simply a design of plastic extrusion machine.
There is the twin screw extruder – but that is a subject for another day.
Single screw extrusion forms a fundamental part of plastic manufacturing process.
It’s a mechanism that builds pressure on melt resign, as it prepares it ready for extrusion.
Figure 2 Single screw turning
Normally, it creates pressure on the polymer, increasing the quality of the melt. As a result, you can produce high quality plastic pipes.
In most cases, single screw is suitable for processing plastic in its pure form.
Depending on the design of the machine, they can be stand-alone systems or, part of a large plastic pipe processing system.
Depending on the design of the single screw extruder for plastic pipes, it may have:
- Barrel
- Single screw
- Control system
- Resign feeding system
- Drive mechanism, among other parts
Don’t worry, I will walk you through all that later in this guide – keep reading.
For now, let focus on yet another important aspect of single screw extruder.
Single Screw Extruder Basics
Perhaps before we go on, you need to understand some basics regarding single screw extruder. This includes understanding why you need to choose a single screw for your plastic pipe processing.
Also, it includes the advantages of utilizing a single screw extruder.
Let’s go through this.
1. Why you need single screw extruder in plastic pipe processing
This is my favorite question when it comes to a single screw extruder machine.
Reason?
You need to know the exact reason why you need any type of plastic pipe manufacturing machine.
Figure 3 Single extruder plastc corrugated pipe extrusion machine
Plastic pipes take various shapes which it would have been difficult to shape without an extruder. Therefore, it implies that having this machine will save you a lot.
Here is a look at why you need a single screw extruding machine.
2. Production of a variety of pipe products
Honestly, here are some pipe products which without a single screw extruder, it would be difficult to produce.
Pipe products like joints and pipe ducts are only available due to the single screw extruder which produces them.
The impact of this is that we can produce a properly functioning system.
3. Availing water to households for use
As human beings, the availability of clean water for drinking is important. Due to advancement in technology, this is made possible.
Water treatment is done in a central place after which water reaches our homes by pumping. Water flows through pipes to reach us.
These pipes are a product of extruder. This implies that we would be traveling for miles to get this precious commodity.
4. Improving agricultural sector
Another reason why a single screw extruder is important to us is in the agricultural sector. Technology enables us to do agriculture without necessarily relying on rainwater.
This requires irrigation which is possible when we have pipes for irrigation. Sprinkling pipes and dripping pipes are available through production by a single screw extruder.
5. Proper human waste management
Living in a clean environment is crucial. Therefore, having a proper waste drainage system is necessary. The availability of PPR and corrugated pipes provides a solution to this. A single screw extruder makes these pipes.
Advantages of a Single Screw Extruder
When it comes to plastic pipe processing, a single screw extruder is an important machine for you to have. However, what makes this extruder to stand out?
Figure 4 HDPE pipes
Well, here are some benefits that you get from using this machine.
- The single screw extruder is of high technology design making it have a well plasticizing function. This allows the use of materials which are in pellets or powder form where melting takes place.
- The extruder has strong stability and high extrusion speed. This is because of the pressure that builds up within the walls as a result of melting.
- With an advanced gear transmission, there is very little noise during the extruding process. On top of this, the extruder machine can handle large production capacity.
Disadvantages of a Single Screw Extruder
Like any machine that is known to man, an extruding machine has got several setbacks. However, you can bear some of the setbacks of using an extruding machine.
Figure 5 Corrugated plastic pipes
To better understand this, let’s have a look at these limitations.
They include:
- Since the transmission of the plastic materials is through friction, there is a limitation when it comes to the feeding performance.
- Some materials like the paste or powder possess difficulties in mixing. This makes using the machine in some processes unsuitable.
- Generally, the single screw extruder is unsuitable when it comes to processes like polymer coloring.
- There is a poor exhaust effect due to the effect the screw has on the exhaust gas region.
- During extrusion, there is an increase in [pressure which causes an increase in the countercurrent. The result of this is that there is a decrease in productivity.
- With time, there is a decrease in space between the screw and the barrel. This is caused by the edge decreasing. The effect of this is that there is a decrease in the number of plastics extruded. The result being plastic overflows minimizing the plasticising effect which in turn reduces the productivity.
Parts of Single Screw Extruder for Plastic Pipes Machine
For you to be in a better position to understand an extruding machine, you need to understand its components. This includes various parts it constitutes and what they do.
Figure 6 Parts of single screw plastic pipe extruder
Even though this machine may look simple and a single unit, the truth is that it is complex. You can note that when you start operating, various parts function as a whole to make the extrusion process a success.
It is therefore imperative that you get to understand these parts and how they relate to each other.
Figure 7 Parts of plastic pipe extruder
In this section, I am going to illustrate these parts to you so that you can understand each part of an extruding machine.
Let’s start off.
a) Gearbox
The gearbox comprises of the gear and the case. The gear is made of alloy steel to provide fatigue strength and wear resistance that the gearbox needs.
On the other hand, the case protects the gear, and as such, it is of high quality cast iron.
Figure 8 Gear box
The purpose of the gearbox is to reduce the motor speed in the screws.
b) Screw and barrel
The screw refers to the circular groove hollow rotating element in the inner part of the barrel of a single screw extruder.
The main functions of the screw are:
- To transport the polymer from the feed hopper to the extruder outlet.
- To bring about the melting of the polymer.
- To carry out any mixing required during the process.
- To generate a stable and homogeneous supply of polymer melt.
The electric motor and the gearbox pre-set the rotation of the screw.
Figure 9 Pipe extrusion
The barrel refers to the part of the single screw extruder that covers the screw. It is normally a corrosion-resistant steel cylinder normally with strong compressive strength and heat.
Generally, the barrel has a length of between 15 to 30 times its diameter. The purpose of this is to make sure that the plastic materials heat up to the required standard.
The screw and barrel work hand in hand to extrude the plastic materials. The ability of them extruding is dependent on
- The manufacturing process of the screw and barrel.
- The nature of the plastic materials.
- Which environment in which the machine operates
c) Electric motor
The electric motor is what powers the functions of the entire extruding machine. This motor converts the electric energy to kinetic energy for the machine to utilize.
The size and nature of the electric motor depending on the extruding machine. Smaller machines tend to have a smaller electric motor, unlike a bigger extruding machine.
Figure 10 Electric motor
However, the important aspect is that you need to ensure that the electric motor functions all the time properly. In case of malfunctions, always ensure you replace the motor with an original one so that your machine can function well.
d) Temperature controller
You can find these controllers in the heating and cooling elements around the barrel. They serve the purpose of controlling the temperature to the one set.
Temperature maintenance is crucial for the extrusion of plastic. At an optimal temperature, the heating of the resins occurs uniformly.
This is important to prevent the stressing and warping of the finished product.
Due to pressure and friction along the barrel walls, the temperature is not always even. That is why temperature controllers are in place to regulate this.
e) Inverter
The purpose of a single screw inverter is to transform direct current to alternating current.
The inverter receives direct current from the mains which are of low frequency and converts it to the alternating currency of high frequency.
The alternating currency provides energy for the functioning of the extruder.
f) Heater
Along the barrel, you will find heaters together with thermocouples. The function of the heater is to control the temperature of the barrel.
For an extruder to work properly, the heaters must cover much of the barrel surface as possible. This minimizes the hot and cold regions along the length of the barrel.
g) Air switch
The electric line of the single screw extruder needs protection in case of electric faults. The air switch does this.
h) Vacuum hopper and loader
A vacuum hopper refers to a cooling tank which operates under low pressure. The aim of this is to control the shape formation of the plastic materials.
The vacuum hopper also helps in the final appeal of the plastic product regarding color. The reason is that the vacuum hopper allows the pipe to cool as it passes through it.
Figure 11 Different parts of single screw pipe extruder
Single Screw Extruder Designs
Before we move on, it is important to have a look at its design.
The design of a single screw extruder is the arrangement of the various parts of the extruding machine.
Also, it entails how these parts relate to one another to work efficiently. That is the aim of this section.
Keep reading.
§ Single screw extruder design
A single screw extruder is made up of five elements. These are:
- Screw
- Extruder drive
- Feeding hopper
- Die
On top of the extruder, there is an upright structure known as the feeding hopper. It has a design that helps it to hold the resins and only allow them to flow steadily.
Gravitational pull assists the resins as the flow to the extruder.
The main element of the single screw extruder is the screw. Typically, it is helical in structure. You can locate the screw inside the fitting barrel.
The barrel can provide heat and cooling effect to the extruder. Its location outside the extruder helps it to regulate the temperature of the single screw extruder.
The gearbox and the speed motor propels the screw forward during operations.
The design of the screw is in such a way that has three areas. The feed, compressor and metering areas.
What happens in the feed area is that the screw holds the resins from the feeding hopper and conveys it to the jacket screw. It is at the jacket screw that the movement of the resins starts longitudinally.
As they move, the barrel which is hot heats up the resins. The friction that occurs within the barrel assists in producing the heat.
Also this friction assists in the movement of the resins forward.
The diameter of the screw is such that it increases as it moves forward while the height of the barrel decreases. This allows few resins to move forward which creates pressure in the barrel. There is a high temperature in this section which causes the resins to melt.
At the tail end of the extruder, there is the die. This serves the purpose of shaping the molten plastic into plastic products.
There are different types of dies depending on the plastic products that you want to extrude. They include:
- Flat film die
- Blown film die
- Tubing die
For the screw to rotate, it needs a power supply. The extruder drive which is an electric motor does this.
Lastly, there is the gearbox which regulates the speed of the screw.
Working of Single Screw Extruder
Now that we have had a look at the design of the single screw extruder and its various parts, it is important to know how the extruder works.
To be honest, you cannot purchase a machine that you are not conversant with how it works. Understanding how it works helps you in cases of a machine breakdown.
Figure 12 Extrusion process
At the end of this section, you will be able to understand how the machine works step by step. In each step, I will explain to you the various components that are there as well as what happens.
Let’s start off.
Before we begin, you need to understand that the different forms of plastic pipes start off as resins. Resins are the raw materials for making plastics, and it comes either in pellet or powder forms.
§ Step 1 – Feeding the resins or pellets
In this step, you feed the resins into the hopper which is at on top of the machine. The reason that is on top of the machine is that it allows for the gravitational pull of the material down the machine.
In case you want to add additives, you can do that in this stage to give time for proper mixing of the materials.
As the materials flow down the machine, they pass through a rotating screw. The pace of the rotating screw slows down the number of materials entering the machine.
It also allows for the mixing of the pellets.
§ Step 2 – Melting of the resins
The screw‘s design is in such a way that there is a heat variance along the barrel. As the materials flow into the screw, they enter the barrel.
The heat in the barrel makes the plastic materials to melt as the materials move forward, the temperature increases.
This ensures the materials melt completely. Also, the increase in temperature along the barrel ensures that the plastic materials melt uniformly.
Another advantage of the gradual increase of temperature along the barrel is that it prevents the materials from overheating. Overheating may affect the quality of the plastic product.
As the molten materials reach the end of the barrel, they encounter a breaker plate. The role of the breaker plate is to filter impurities as the plastic move along the screen.
In case you want to achieve maximum uniform melting of the plastic materials, you can increase the number of the screen. Another way of that you can achieve this is by manipulating the porosity of the screen plates.
§ Step 3 – Actual extrusion process
When melting is complete, the molten plastic moves to the die through the barrel. Due to pressure, there is a force here that forces the materials into shapes. A mandrel which is at the center of the extrusion channel separates the plastic.
Pumping of air at high pressure into the mandrel structure is done to prevent the plastic from collapsing as it moves along the die.
You need to pay particular details to the die since any fault at this stage will create problems for your final product.
§ Step 4 – Cooling it down
After passing through the die, your plastic passes through the cooling zone. There are different types of cooling systems depending on your machine.
These are air and water cooling systems.
Air cooling system utilizes air to cool the barrel section of the extruder. It is common in plastic materials that don’t need much heat.
Air cooling system allows for the gradual decrease in temperature of the plastics and the barrel.
Water cooling system is common when the heating materials require a sudden change in temperature. You need to maintain the water cooling system to reduce fouling regularly.
§ Step 5 – Final finishing procedures
This is the last step which involves putting the final touches on your plastics. This includes drilling, printing, bending or cutting.
Having had a look at the principles of a single screw extruder, here are the common extrusion processes.
Figure 13 Summary of plastic extrusion process
§ Blown film extrusion
This process is useful when making plastic products like storage and grocery bags. The fitting of the cylindrical die is in an upright position. This helps in dragging the molten plastic up as it shapes and cools.
§ Co-extrusion
In this process, there is a simultaneous extrusion of a few layers of materials. For this to happen, more than one extruder feed the single screw extruder with different types of resins.
§ Over jacketing
It is a type of extrusion process where extrusion is done to coat a product. This is done to offer a protective layer to the product.
Cable jacketing is a common application of this process.
Main Applications of Single Screw Extruder in Plastic Pipes Industry
Yes, now you have the idea of what an extruding machine is and how it works, but where exactly do you use this machine?
This is an important question you need to ask yourself before you start off in the pipe making industry.
This section answers this question. You will learn which pipes exactly you can manufacture using the extruding machine.
Let’s begin.
§ Manufacture of PE pipes
One of the main application of a single screw extruder in the plastic industry is in the manufacture of PE pipes.
Figure 14 PE pipes
PE pipes refer to pipes produced from ethylene polymerizations.
The use of these pipes is in the following areas.
- Supply of water for use in mining
- Supply of irrigation water.
- Supply of mineral slurry
- Supply of water for domestic use.
- In the making of gravity and vacuum sewer systems.
The properties that the PE pipes have makes it suitable for use in the above areas. These properties include:
- Light in weight
- Chemical resistance
- Durable with long service lifespan
- Flexibility
- Overall toughness
Another form of PE pipes is the HDPE pipe. HDPE pipe is similar to the PE pipe with the difference arising from the density. HDPE has a high density than the PE pipe.
§ Manufacture of PPR Pipes
Another use of this machine is the manufacture of PPR pipes. These refer to polypropylene random copolymer pipes.
Figure 15 PPR pipes
One of the main advantages of the PPR pipes is their resistance to heat. This makes them suitable for use in residential cold or hot water systems.
Other uses of this pipe include:
- Underground heating system
- Chemical materials and industrial water conveying system.
- Pire and sanitary water pipelines.
- Recycling system for hot water.
- Air compressing system.
The manufacturing of these pipes entails equipping them for fusion welding for joining to each other.
§ Corrugated Pipes
You can also use this machine in the manufacture of corrugated pipes. These refer to pipes that contain ridges.
Figure 16 Corrugated pipes
These furrows and ridges run parallel to the pipe hence encircling the whole pipe.
A corrugated pipe has several advantages which include the following:
- It has a long lifespan which ensures maximum performance.
- The furrows and ridges make it appear light in weight. However, they are very strong.
- These pipes have less leakage probability due to the strong material that makes it.
- These pipes have less operational cost when you compare to the other pipes during manufacturing.
Support Equipment for Single Screw Plastic Pipe Extrusion
Some of the main support equipment you need in when using single screw extruder include:
§ Extruding Die
The extruding die is that part of a single extruder that forces the molten materials to form plastic shapes. Its location is towards the end of the screw.
Some functions of the extruding die include:
- It shapes the molten plastic to give it the shape it needs at a specific rate.
- It gives the pipe the physical properties by controlling the product’s molecular orientation.
- It controls the surface aesthetics of the product
The advantage of the extruding screw is that you can customize it to produce the kind of plastic product you need.
§ Cooling Tank
A tank that typically contains water through which the pipe passes through after extrusion for cooling.
These pipes are normally hot after extrusion hence need to reduce the temperature to minimize the chances of deformation.
§ Plastic Pipe Cutter
A plastic pipe cutter refers to a sharp knife edge whose purpose is to cut plastic pipes from sheet stock. Another use is that of trimming the plastic shapes.
§ Plastic Pipe Stacker or winder
After completion of the plastic production, you will need a place to hold them together. That is where the function of a plastic pipe stacker comes in.
It refers to equipment for holding the pipes together for proper arrangement. For pipes that have a diameter of below 110mm, you can use a winder.
The winder serves the same function as the stacker.
Single Screw Extruder Specifications
If you want to understand the specifications of a single screw extruder, you need to understand the individual models.
Overall, single screw extruders belong to two categories which are:
§ High efficient single screw extruder
A common characteristic of these types of screws is that they have an L: D ratio of 38:1. An L: D ratio refers to the ratio of the length of the flight length of the screw to the outside diameter of the screw.
Figure 17 Highly efficient single screw extruder
Another common aspect of this screw is that their increase rate when you compare with G1 is 20%. The only exception to this is the KPM 120/38 which has a rate of 30%
Let’s have a look at the individual models
- KPM 60/38
This model has a screw diameter of 60mm and an L: D ratio of 38:1. The KPM 60/28 has a motor power of 110kw while its output performance is 465kg/hr.
- KPM 75/38
This model has an output performance of 650kg/hr while its motor power consumption is 160kw. When you look at the screw diameter, you will notice that it has a diameter of 75mm.
The L: D ratio of this model is 38:1.
- KPM 90/38
You can identify this kind of a model by checking for its screw diameter which has to be 90mm. The output performance of this model is 1100kg/hr while it operates on motor performance of 280kw.
- KPM 120/38
A characteristic of this model is that it has a screw diameter of 120mm and a motor power of 315kw. The output performance of this model is 1300 kg/hr. and an L: D ratio of 38:1
§ Normal standard single screw extruder
The normal standard single screw extruder has a common characteristic of having an L: D ratio of 33:1. They also have a waste rate of 20% when you compare them to G2.
Figure 18 Standard single screw extruder
The models in this categories include:
- KPM 60/33
The KPM 60/33 model has a screw diameter of 60mm and an L: D ratio of 33:1. They also have a motor power consumption of 110kw.
- KPM 90/33
The characteristics of this model are that it has a screw diameter of 90mm an L: D ratio of 33:1. The output performance of this model is 750kg/hr while the motor power consumption is 250kw.
- KPM 120/33
This model has a screw diameter of 120mm and an L: D ratio of 33:1. When you look at its output performance, it outputs 900kg/hr.
This power consumption of this model is 315kw.
BENK Single Screw Extruder
BENK single screw extruder is an extrusion machine that manufactures plastic pipes. This extruding machine has the characteristics of a single screw inside the barrel.
Figure 19 BENK Single screw extruder
BENK single screw extruder is quite affordable, and there is a guarantee of quality with this product.
The parts of BENK single screw extruder are original and quality parts which include the gearbox, screw, and barrel. Other parts are the inverter and the temperature controller.
You can use BENK single screw extruder to produce PE pipe, PPR pipes, HDPE corrugated pipes.
You can choose from two of our main variance of BENK single screw extruder machines. We have the high efficient single screw extruder whose production capacity is higher. These type of extruders save on energy.
The other type is the normal standard single screw extruder. When you compare these types of the extruder to BENK high efficient single screw extruder, their production capacity is a bit low.
Whichever type of BENK single screw extruder you choose, we will gladly ship it to you at a reasonable price.
Figure 20 BENK Single screw extruder
We can customize the BENK single screw extruders to fit your purpose. What you need to do is to contact us and let us know the pipe size you want to produce.
Also, you can let us know the raw materials and what your production capacity per hour is and we will design an extruder that fits your needs.
At BENK, we supply and install these extruders for our clients when they purchase from us. On top of this, we offer support services including training and maintenance in case of malfunctions.
Conclusion
The single screw extruding machine plays an integral part in the manufacturing of plastic pipes. As such, you need to engage a well-known and trusted manufacturer for purchasing.
You need not look further for this kind of a manufacturer.
BENK is here for you. With many years in the manufacturing industry, we guarantee you quality extruding machine.
And by the way, our team of professional engineers is always ready to do the installation for you. In addition to this, we offer support staff to train your staff if you require it.
All this we offer at a reasonable price which fits the pockets of our clients.
Get in touch with us today and get yourself an extruding machine that will guarantee production for a long time.