SPC vinyl floor making machine
Extruder | SJZ80 conical twin screw extruder |
Mold | T-die from JC time brand |
Forming machine | Three-roller |
Surface hot transfer | Two rollers up three roller |
Cooling bracket | Aluminum pipe with side cutting knife |
UV protect film | up haul-off |
Haul-off | two rollers |
Cutter and stacker | No-noise cutter and automatic arm |
Control system | Siemens touch screw and Siemens PLC |
Electric parts and motor | Siemens Ac motor, Schneider and Ormon electric |
Your first choose for SPC vinyl floor making machine manufacturer in China
BENK SPC vinyl floor making machine also named stone plastic composite floor making machine which is used plastic extrusion technology to plasticize PVC with caco3 and other additives into SPC flooring sheet.
SPC vinyl floor making machine can make 3-8mm thickness, 1220mm width stone plastic sheet, production capacity can from 400-1000kg/h, and vinyl floor machine can worked for 24 hours without any maintain.
Stone plastic floor making machine is a new and advanced technology to be used to make stone plastic floor or rigid vinyl plank, our stone plastic extruding machine can make rigid SPC core, printing decoration layer and transparent wear-resistant layer by one time, it can save the time, labors and waste for you.
BENK SPC flooring extruding machine is consisted by conical twin screw extruder, extrusion die, four roller calender, cooling bridge and trimming device, haul-off, precious cutter and automatic stacker.
BENK stone plastic plank extruding machine has advantages of high precious controlling system, high efficient and easy operating.
BENK vinyl floor making machine can make LVT(luxury vinyl tile), LVP (luxury vinyl plank), WPC(wood plastic composite) floor and SPC floor(stone plastic floor) to be used in home floor, hospital floor, shopping mall floor and many indoor floor.
- Production images
- Data Sheet
- Testing Video
- Send Enquiry

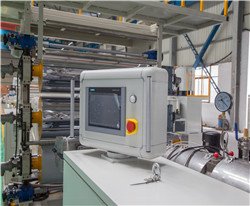





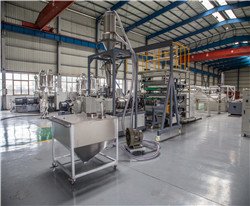
Data of SPC vinyl floor making machine:
Extruder | SJZ80/156 |
Output | 350-400KG |
Finished sheet wide | 1220mm |
Finished sheet thickness | 1-8mm |
Main motor | 75KW |
Control | PLC |
SPC Vinyl Floor Making Machine- The Complete Guide for Importers in 2018
Chapter 1: What is SPC vinyl floor making machine?
Do you want to the most popular SPC vinyl floor in the world? It can instead of wood floor and it is much cheaper than wood floor.
Benk is here for you.
SPC vinyl floor making machine is used to make vinyl floor, the main raw material of vinyl floor is PVC(poly-vinyl chloride), so we call it vinyl floor.
SPC vinyl floor making machine is using plasticizing extrusion technology to make 1220mm width PVC sheet, the PVC sheet has three layer, the base layer is vinyl core, the middle layer is printing decoration film, and the top layer is transparent PVC film wear-resistance.
Figure 1: Structure for SPC floor
Before the middle layer and top layer is separated, now you can buy the combinated film from China, we can recommend the manufacturer for you.
You also can see the anti fade UV coating, it is made by UV coating machine which is off the production line.
PVC floor was start from Europe and America, as vinyl floor is non-toxic and harmless material floor compare with some wood floor, then many clients would like to choose vinyl floor.
1. What plastic floor can made by SPC vinyl floor making machine?
1.1 LVT: luxury vinyl tile,
1.2 LVP: luxury vinyl plank
1.3 Vinyl floor
1.4 Vinyl plank
1.5 WPC: wood plastic composite( Because we mix wood powder with plastic, it is very difficult to recycle, we donot add any wood powder in our formulation when we make WPC floor)
1.6 SPC:stone plastic composite, Europe and American call it RVP(rigid vinyl plank)。
Chapter 2: How to make SPC vinyl floor?
When you see the most famous vinyl floor in the world, I am sure you must want to know how to make it, and what is it advantages?
Process 1: Mixing
Automatic metering according to raw material ratio → high-speed mixer hot mixing (hot mixing temperature: 125 degrees, function: It is a mixture of various materials, remove the moisture in the material) → enter the cold mix (to cool the material, Prevents caking and discoloration, cold mixing temperature: 55 degrees. )→mixing the homogeneous material by cooling;
Figure 2: Mixer
Process 2: Extrusion line
Adding to the twin-screw extruder for heating and extrusion → into the sheet die extrusion molding, the formed sheet
The material is passed through a four-roll calender, and the substrate is thickened → paste film → adhesive layer → cooling → cutting and automatic stacker
Figure 3: SPC floor extrusion line
Process 3: UV tempering
Surface UV→tempering (tempering hot water temperature: 80~120 degrees; cold water temperature: 10 degrees)
It is used to make UV coating on the top layer of SPC floor, it can make floor more smooth and shinning and more wear-resistance.
Figure 4: UV coating machine
Process 4: slitting and slotting + packaging
Slitting → Slotting, Trimming, Chamfering → Inspection → Packaging
Slitting machine is cut the 1220mm width into small width sheet, like 190mm width, 180mm width.
Figure 5: Slitting machine
The slotting machine is used to groove mill in the four side of SPC floor, the mill can help you to install the SPC floor easily.
Figure 6 : Slotting machine for SPC floor
After the SPC floor finished, you must want to know how to install it, here is the video for installation, you can know it will be easier than you think.
Chapter 3: What is the parts for SPC vinyl floor making machine?
SPC vinyl floor making machine is combinated by PVC extrusion process and calender process together to make 2-8mm thickness vinyl sheet.
The vinyl sheet is already covered by decoration film and wear-resistance film, the decoration film and wear-resistance film is stick with the vinyl sheet by heat online.
When we want to make the SPC floor, we need the auxiliary machines to do it, like UV coating machine, cutting machine and slotting machine.
In this chapter, we will discuss about the extrusion, so what parts will be in the vinyl floor extrusion machine?
- Conical twin screw extruder:
According to the production capacity, you can choose the extruder by youself, we have three types for choosing now, which are cm80, 92, 110 extruder.
Normally, we will assemble cm80 extruder into production line, and most of clients want to save cost for themselves in the beginning.
Figure 7: Extruder
- Extrusion die
Extrusion die is made by 40CR, it is hanger design inside of molds, we can adjust the thickness of SPC floor sheet from 2-8mm by screw in the die.
The mold is very precious and durable, it can be used for more than 10 years.
The size of extrusion die is 1220mm width normally, we also can design the width for you as per your requirements.
Figure 8: Extrusion die
- Three roll or four roll calender
Three or four roll calender is used to keep the temperature of stone plastic sheet, and make the surface of PVC sheet more smoothly and more evenly.
The temperature of roller is controlled by oil temperature controller, we can control the temperature preciously.
There is one roller is embossed roller, the other three are mirror roller, each roller can be controlled by motor up and down separately.
Figure 9: three or four roll calender
- Cooling bride and trimming device
Cooling bridge is used to cool the vinyl sheet, and trimming the two sides of vinyl sheet, it is made by steel pipe and iron frame.
Figure 10: Cooling bridge
- Two roll haul-off
Figure 11: Two roll haul-off
Two roll haul-off is made by two rubber rollers, the up and down is controlled by cylinders, and the speed is controlled by PLC controller, the speed can be adjusted preciously, so it will be easy for you to open the machine.
- Automatic Robert arm stacker
Figure 12: Automatic Robert arm stacker
Automatic Robert arm stacker is very precious to be controlled by PLC, and it can save labor for you with low power consumption, and it also can protect the vinyl sheet with Robert arm stacker, because the vinyl floor is very thin, it is very easy to be damaged by hand or your staff.
Chapter 4: Classification of LVT, WPC floor and SPC floor?
At present, PVC sheet flooring can be made into two kinds, one is that the pattern material from the bottom to the surface is the same homogeneous and transparent floor. If the surface is burnt out or scratched, it can be repaired with a sander. . The other is that the uppermost layer is a pure PVC transparent layer and then a combination of a printed layer and a foamed layer is added below. It can be seen that the same quality of the core material is much superior to the composite type.
From the morphological point of view, it is divided into coil floor and sheet floor; the products highlighted in this article: LVT, WPC floor is semi-rigid sheet plastic floor, and SPC (RVP) floor is hard sheet floor. At present, there are three main types of LVT flooring: vinyl locking, dry back, loose laying. From another perspective, PVC flooring can be divided into: Dry Back lock (Loose lay). At the same time, WPC wood plastic flooring and SPC stone plastic flooring are also in the active promotion and high-speed development stage in the domestic and foreign markets.
4.1 Comparison of dry back and loose lay in plastic flooring
4.1.1 Same point: Both belong to PVC floor, the specifications are the same, and some parts are the same size;
Dry back mainly has 942*157, 1227*157, 1227*187, 1227*235, 914.4*101.6, 470*470, 608*308 (unit: mm) these eight specifications;
The loose lay mainly has 942*157, 1227*157, 1227*187, 1227*235, 470*470, 608*308 (unit: mm).
Click mainly has 936*150, 1220*150, 1220*180, 1220*228, 1500*228, 600*300 (unit: mm) These specifications, pay attention to the comparison with dry back.
WPC currently has two specifications 1217*146, 1217*178, 596*296 (unit: mm).
SPC mainly has: 1210*150, 1210*181, 203*1219, 178*1219, 152*1219 (in millimeters)
4.1.2 Differences
- Installation method: dry back requires the use of glue, etc., also known as glue down, loose lay directly on the pavement (loose lay on the bottom layer with a layer of black leather, placed on the plane can not move.)
- Thickness: dry back, we only only starts from 2.0mm thick bottom. If it is lower than this specification, loose lay is generally consistent with Click 4.0mm, 5.0mm
- Wear-resisting layer: Under normal circumstances, we are now doing 2.0mm and 2.5mm thick Dry back, wear-resistant 0.1mm-0.5mm, 3.0mm thick Dry Back, wear-resistant 0.1mm-1.0mm, 2.0mm And the principle of 2.5mm can do more than 0.5mm wear resistance, but it is not cost-effective. In addition, the formula of the base material and the middle material have to be changed and tested. Now the factory basically does not do; loose lay now, The wear layers of 4.0mm and 5mm are basically only wearable for 0.3mm and 0.5mm, for the same reason.
- Price: dry back is cheap, loose lay is more expensive
- Health time: dry back requires 24 hours of health after tempering. Loose lay is the same as the lock series, which takes 48 hours.
F: The flexibility of the two is different. The loose lay product is obviously much softer than the dry back. Such characteristics can also be used as a distinguishing feature. At the same time, the most obvious is that there is a layer of black leather at the bottom of the loose lay, which can be distinguished by soft and hard using a nail scraping test.
4.3, the composition of the plastic floor
PVC floor composition: PVC resin powder, stone powder, stabilizer, carbon black, the main components are polyvinyl chloride and stone powder.
The plastic floor is composed of a backing layer, a core layer, a glass fiber, a decorative paper and a wear layer from bottom to top.
4.4, PVC certification
At present, PVC products are certified by Floor score, DIBT, CE, ISO14001: 2004 and ISO9001: 2008, TÜV Rheinland.
4.5, PVC’s most critical product indicators
- Stability: Product shrinkage expansion rate 80 ° C 6 hours. 0.25%, 0.15% (line standard)
- Heating warpage: 80 ° C 6 hours EN < 2 mm; Enterprise standard: 1.2 mm (dryback); 1.0 mm (click); 0.5 mm (loose lay)
- Lock pull: normal temperature (23 ° C) 5.0mm> 13-15kgs / 5cm.
- 4.2mm>12kgs/5cm.
- If the short side is V buckle, 4.2mm>15-18kgs/5cm.
- Peeling strength: the bonding strength of the color film and the middle material
- Scratch resistant, wear resistant
- Brightness: 10+/-2.
4.2 The advantages and disadvantages of LVT floor:
Six major advantages:
1. Green environmental protection
The main raw material for the production of PVC flooring is polyvinyl chloride. Polyvinyl chloride is an environmentally friendly and non-toxic renewable resource. It has been used in people’s daily lives, such as tableware and medical infusion tube bags. Its environmental protection is unnecessary worries.
2. Super wear-resistant
The surface of the PVC floor has a special layer of PVC wear-resistant layer, and its wear-resistant number can reach 300,000 rpm. According to the different thickness of wear resistance, it can be used for 5-10 years under normal conditions.
The thickness and quality of the wear layer directly determine the use time of PVC floor. The standard test results show that the wear layer of 0.55mm thick can be under normal conditions. After more than 5 years, the 0.7mm thick wear-resistant layer is enough for more than 10 years, so it is super wear-resistant.
Because of its superior wear resistance, PVC flooring is becoming more and more popular in hospitals, schools, office buildings, shopping malls, supermarkets, transportation and other places with large traffic. (The wear resistance of the wear layer is currently mainly measured by measuring the loss, that is, the mass reduction)
3. High elasticity and super shock resistance
The PVC floor is soft in texture, so it has good elasticity. It has good elastic recovery under the impact of heavy objects. At the same time, PVC floor has strong impact resistance, and it has strong elastic recovery for heavy impact damage without damage. The excellent PVC floor can minimize the damage of the ground to the human body and can disperse the impact on the foot. The latest research data shows that the staff fell when the excellent PVC floor was paved in a space with a large flow of people. And the rate of injuries is nearly 70% lower than other floors.
4. fire retardant
The qualified fireproof index of PVC floor can reach B1 level, and the B1 grade means that the fire performance is very good, second only to stone. It is extinguished from the fire.
5. Easy maintenance
The maintenance of the PVC floor is very convenient, and the floor is dirty and wiped with a mop. If you want to keep the floor lasting, you only need to polish it regularly, and the maintenance frequency is much lower than that of laminate flooring.
6. Waterproof and moisture proof
Since the main component of PVC flooring is vinyl resin and has no affinity with water, it is naturally not afraid of water. As long as it is not soaked for a long time, it will not be damaged; and it will not be mildewed due to high humidity.
Two disadvantages:
Non-natural materials, high requirements for the base floor (the base layer must be flat, solid and dry when the LVT floor is laid, the surface of the plastic floor is smooth, the yin and yang angles are square, no ribs, no oil, dust and impurities).
4.3 WPC floor
WPC combines the waterproof and stability of LVT and is also easy to install like a laminate flooring.
Figure: WPC floor
The addition of cork and EVA mats, foot feel and sound insulation are better than LVT’s lock floor.
WPC uses environmentally friendly materials that are more environmentally friendly than laminate flooring.
Conclusion: WPC between LVT and Laminate, both have the advantages.
4.3.1. Composition
WPC: Wood Plastic Composition=LVT Layer + WPC Core
1 WPC LVT layer and WPC layer are glued, the peel strength is still very good, even better than the LVT color film layer and frosted sheet after hot pressing
2 WPC stability is better than PVC:
The WPC floor was taken at a high temperature of 80 degrees plus or minus 2 degrees for 6 hours, and was taken out at a normal temperature of 23 plus or minus 2 degrees, and observed at a humidity of 50% for 24 hours. Concluded as follow:
Length shrinkage is 0.08%
Width shrinkage is 0.05%
Warpage: 0.25mm
LVT: 0.08-0.15%
Warpage: 0.5-1.2mm
- the advantages of WPC
WPC Engineered Vinyl Flooring – WPC’s price is gold-grade, WPC’s price of 5.5mm is basically the same price level as Vinyl’s 5.0mm lock and glue-free product, but higher than the magic buckle, and far higher For washing glue and ordinary PVC floor (brush type);
WPC installation cost is far lower than ordinary brushed PVC floor, lower than ordinary PVC lock floor, and glue-free PVC floor, magic buckle and washable rubber PVC floor installation cost is not much different;
The waterproof of WPC is quite good, and the waterproof of this layer of wood plastic is also very stable. On the contrary, magic buckle, washing glue, ordinary brush-type PVC floor, because of the glue involved, the waterproof effect is general;
Because of the ease of installation, WPC is relatively easy to use because it is the installation method of Angle-Tap. It is suitable for DIY. Of course, the Dry back that needs to be brushed separately is the worst at this point.
The WPC floor is definitely good for quietness and foot feel, especially WPC flooring with cork or EVA mats;
WPC is also very good at environmental protection, including formaldehyde emission, heavy metals, especially Reach test, and 144 items are all passed.
WPC has good sound absorption effect and good energy saving, which makes indoor energy saving up to 30%.
WPC is simple to install, easy to construct, does not require complicated construction techniques, saves installation time and cost
WPC flooring is weak in terms of recyclability after use, because WPC (Wood Plastic composite) cannot be recycled and reused. PVC flooring of other products can be reused as a return material.
- Several issues that need to be paid attention to in WPC and customer communication
(1) Because the LTV layer of WPC is generally only 1.5mm thick, the plate pattern should be as flat as possible. Do not do the hand and the classic slate (slate pattern).
(2) The cost of the 6.0MM wood-plastic layer is 5.0 dollars higher than the 5.0MM wood-plastic layer.
WPC+2.0mm EVA Form: Price +USD1.00SQM
WPC+1.5mm Cork: Price +USD1.50SQM
4.4 Stone plastic floor SPC:
SPC floor
SPC (Stone plastic composite) is a new environmentally-friendly floor based on high-tech, featuring zero formaldehyde, mildew proof, moisture proof, fireproof, insect proof and simple installation.
SPC floor is extruded from the extruder with T-die to extrude the PVC substrate, and the three-roll or four-roll calender is used to respectively wear the PVC wear-resistant layer, PVC color film and PVC substrate, and heat-fit and emboss the product once.
The process is simple, the fit is done by heat, and no glue is needed. SPC flooring materials use environmentally friendly formulations and do not contain harmful substances such as heavy metals, phthalates, methanol, etc., in accordance with EN14372, EN649-2011, IEC62321, GB4085-83 standards.
It is very popular in developed countries in Europe and America and in the Asia Pacific market. With its excellent stability and durability, the stone-plastic floor not only solves the problem of moisture deformation and mildew of the solid wood floor, but also solves the formaldehyde problem of other decoration materials.
It has a wide range of color patterns to choose from, suitable for indoor home improvement, hotels, hospitals, shopping malls and other public places.
SPC flooring
SPC floor shrinkage: ≤1‰ (after tempering), ≤2.5‰ (before tempering treatment), (shrinkage test standard: 80°C, 6 hours standard);
SPC floor density: 1.9~2 tons/m3;
SPC floor advantages: SPC floor physical indicators are stable and reliable, and chemical indicators meet international and national standards;
SPC floor defects: SPC floor density, heavy weight, high transportation costs;
Production of SPC flooring compared with LVT and WPC flooring: SPC flooring processing and manufacturing process is simple.
Advantages of SPC eco-friendly flooring:
SPC flooring is a new environmentally friendly composite product with the following advantages:
(1) Waterproof and moisture proof. It fundamentally solves the problem that wood products are prone to decay and swelling after being damp and damp in a humid and multi-water environment, and can be used in an environment where traditional wood products cannot be used;
(2) Insect and termite prevention, effectively eliminate insect harassment and prolong service life;
(3) Colorful, there are many colors to choose from. It has both natural woody texture and wooden texture, and can be customized according to your own personality;
(4) It has strong plasticity, can realize individualized style very simply, and fully reflects individual style;
(5) High environmental protection, no pollution, no pollution, and can be recycled. The product does not contain benzene and formaldehyde. It is an environmentally friendly product. Recycling greatly saves the amount of wood used, and is suitable for sustainable national policy for the benefit of society;
(6) High fire resistance. It can be effectively flame retardant, the fire rating is up to B1 level, it will self-extinguish in case of fire, and it will not produce any toxic gas;
(7) Good process ability, can be ordered, planed, sawn, drillable, surface painted.
After we know the different between between SPC floor and LVT and WPC, then we can understand why SPC floor is so hot in the market, so does the SPC floor extruding machine.
Chapter 5: What auxiliary machines need for making SPC floor?
For making the SPC floor, we have mentioned the main machines in above words, so what auxiliary machines need for making SPC flooring.
Here, we will talk about some small auxiliary machines to recycling the waste SPC floor, so what are they?
They are plastic crusher and pulverizer.
- Crusher
We have two types for crusher which are PC series and SWP series, for start the SPC floor extruding machine project, we only suggest PC series for our clients, as its price is cheap and save electricity for you in the production.
PC series crusher
- Pulverizer
There also some small to be choosed, if you want to know more, you can check with our sales department
Plastic pulverizer
Chapter 6: What benefits you can get when you buy SPC floor extrusion line from them?
- Longer warranty:
13months since date on bill of lading
- Professional service:
High cost formulation for SPC floor, high efficient SPC extrusion line, overall services on testing and after-sale service.
- Special experience:
First to guarantee the quality of SPC floor extruding machine and other supplementary machines, trustable advice on your factory design and investment.